Understanding MRP Inputs and Outputs for Efficiency
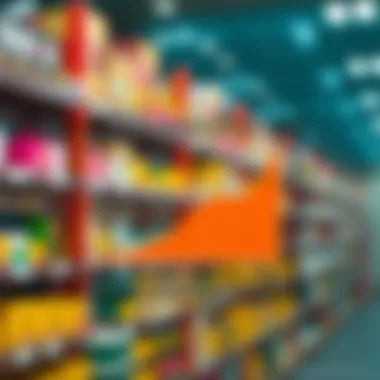
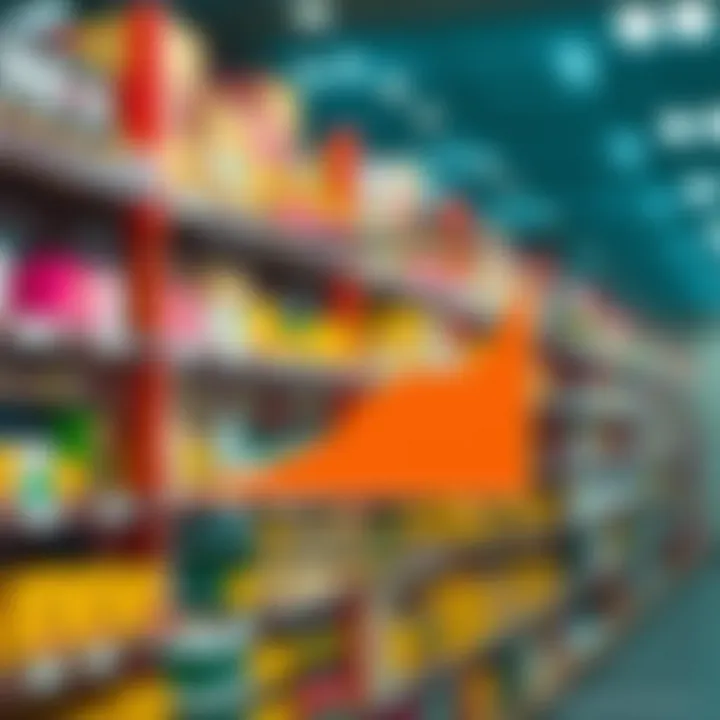
Intro
In this article, we will dig into the core elements of MRP, exploring the critical inputs—like inventory levels, demand forecasts, and lead times—and how they interact to produce meaningful outputs. This journey aims to equip investors, financial advisors, analysts, accountants, and entrepreneurs with the nuanced insights they need to leverage MRP principles effectively in their own ventures.
We’ll also delve into the relationship between MRP systems and operational efficiency, shedding light on how decision-making is influenced by these elements. By the end of this article, you should feel well-prepared to apply the knowledge gained in your ongoing business strategies and investment decisions.
Preface to MRP
Material Requirements Planning, commonly known as MRP, represents a cornerstone in modern manufacturing and inventory management practices. Understanding the framework and functionality of MRP is not merely useful; it’s critical for anyone involved in production processes, be they investors, financial analysts, or entrepreneurs.
At its core, MRP aims to ensure that materials are available for production while maintaining the lowest possible level of inventory. This delicate balance can lead to significant cost savings and efficiency gains. Moreover, as the market evolves, the ability to adapt production schedules based on demand forecasts and inventory levels becomes increasingly vital. In the often unpredictable landscape of manufacturing, a robust MRP system can be the difference between success and failure.
"The right material to the right place at the right time."
This simple yet profound mantra encapsulates the essence of MRP, making it a compelling focus for businesses striving to enhance their operational performance.
The benefits extend beyond material management into broader realms of business strategy. With proper MRP implementations, companies can reduce lead times, improve customer satisfaction through better delivery schedules, and ultimately enhance profitability. But to reap these benefits, a solid comprehension of MRP’s inputs and outputs is necessary.
Definition of MRP
MRP, or Material Requirements Planning, is a systematic process that assists manufacturers in planning, scheduling, and controlling inventory. It's primarily designed to manage manufacturing processes efficiently by aligning inventory levels and production schedules with demand forecasts. MRP systems utilize various inputs—including inventory records, bill of materials, master production schedules, and demand forecasts—to determine material requirements and ensure that materials are available as needed for production. Through sophisticated algorithms, MRP can also project future needs based on historical data and trends, allowing businesses to plan ahead instead of merely reacting to changes in demand.
History and Evolution of MRP
The roots of MRP trace back to the late 1960s when manufacturing saw a shift towards more quantitative approaches to manage production processes. Initially, MRP systems were developed as computer-based solutions to tackle inventory management issues that arose from the increasing complexity of supply chains. The introduction of MRP II in the 1980s expanded the scope by integrating financial and operational data, enabling businesses to align production with their overall business strategy. Today, as technology advances, many businesses are integrating MRP with enterprise resource planning (ERP) solutions, making it a vital tool in realizing an organization’s operational efficiency.
Importance of MRP in Manufacturing
The relevance of MRP in the manufacturing sector cannot be overstated. It serves several critical functions:
- Inventory Optimization: MRP allows companies to maintain optimal inventory levels, preventing overstock and stockouts.
- Production Efficiency: By scheduling production runs, MRP minimizes downtime and effectively allocates resources.
- Cost Reduction: Through improved inventory management and reduced waste, MRP contributes to lower overall costs.
- Enhanced Decision-Making: With a well-structured MRP system, businesses can make informed decisions based on real-time data about demand and supply.
As the manufacturing landscape evolves, adopting effective MRP processes becomes a compelling necessity for businesses that want to thrive in a competitive market.
Key Inputs of MRP
Material Requirements Planning (MRP) serves as the backbone of modern manufacturing and inventory management. The inputs to the MRP process are crucial because they lay the groundwork for effective planning, capacity management, and efficient production cycles. Understanding these inputs helps organizations streamline their operations and minimize waste, which is a significant concern for investors and entrepreneurs. As accurate and timely inputs are vital, delving into these key components enhances one's ability to make informed decisions regarding resource allocation and production strategies.
Bill of Materials (BOM)
The Bill of Materials (BOM) is essentially a comprehensive list that itemizes all the raw materials, components, and parts necessary to produce a finished product. Think of it as a recipe; just like baking requires specific ingredients in exact quantities, manufacturing also relies on precise information about components. An accurate BOM not only helps in ensuring that all parts are readily available for production but also prevents costly delays that can stem from shortages or incorrect orders.
Moreover, the BOM reflects the relationship between various parts. For example, if producing a bicycle, the BOM will include items like wheels, frame, gears, and cables, along with the quantities needed. A well-structured BOM can significantly reduce the risk of production hiccups.
Inventory Records
Maintaining Inventory Records is another cornerstone in the MRP inputs. These records track the current levels of inventory, categorizing items into raw materials, work-in-progress, and finished goods. Regular updates to these records ensure that decision-makers have real-time visibility into stock levels, allowing for more agile responses to changing production needs.
Without up-to-date inventory records, organizations face the risk of overstock or stockouts, both of which can severely impact the bottom line. Regular audits and real-time logging of inventory changes can form the cornerstone of an efficient inventory management strategy that safeguards investment.
Master Production Schedule (MPS)
The Master Production Schedule (MPS) outlines what products need to be produced, in what quantities, and when they should be produced. This schedule acts as a roadmap for the entire production process. For investors focusing on operational efficiency, a well-defined MPS is essential as it aligns production with customer demand.
If the MPS specifies that a certain batch of products is required in two weeks, MRP can automatically calculate the necessary inputs, sourcing from BOM and Inventory Records while accommodating lead times. It's a critical component that not only optimizes resource use but also bolsters planning accuracy.
Lead Times
Lead Times represent the duration taken from ordering a component to its arrival at the production facility. Different components come with varying lead times, influenced by supplier capacity, shipping schedules, and production schedules. Understanding lead times is key to crafting efficient production plans.
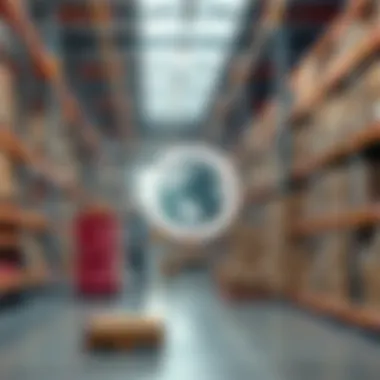
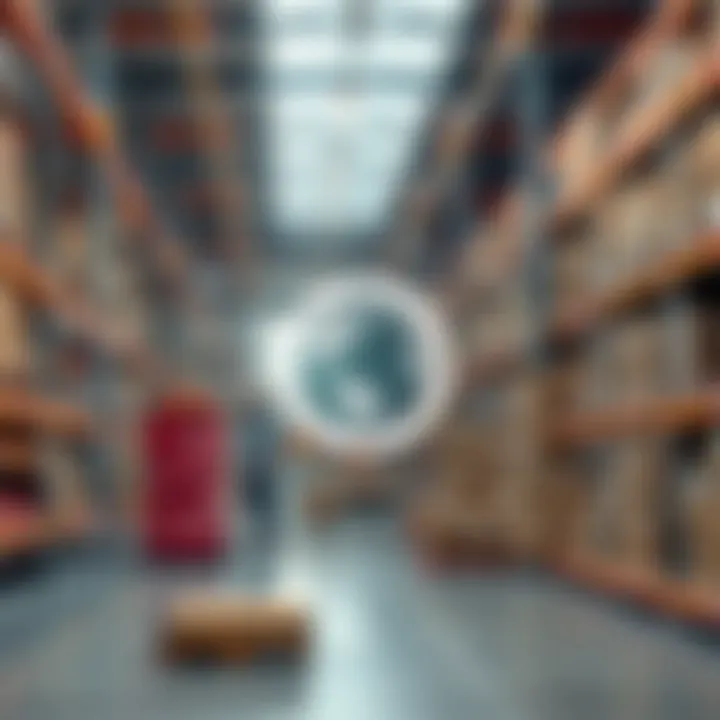
By accurately estimating lead times, businesses can order the necessary materials ahead of time, minimizing idle machines and labor costs while also enhancing overall productivity. Moreover, investors should see lead times as opportunities to negotiate better contracts with suppliers that could lead to improved terms.
Demand Forecasts
Lastly, Demand Forecasts are pivotal in predicting customer demand for products. These forecasts, built from historical sales data, market trends, and even seasonality, provide companies with a glimpse into future requirements. Understanding demand patterns enables businesses to adjust their production schedules accordingly, avoiding overproduction or shortages that can erode profits.
A thorough approach to demand forecasting helps businesses align their resources with market needs, optimizing inventory levels while ensuring customer satisfaction. For any business seeking to bolster its market position, investing time in understanding and applying demand forecasts can pay dividends.
Accurate inputs in the MRP system can lead to more reliable outputs, thus directly impacting profitability and operational efficiency.
Process of MRP
The Process of Material Requirements Planning (MRP) serves as the backbone of manufacturing efficiency. It enables businesses to translate their demand forecasts into actionable production plans. While it may seem a straightforward task on the surface, the process encompasses a myriad of elements that work harmoniously to streamline operations. With the rising complexities of global manufacturing, understanding this process is essential for anyone looking to optimize productivity and inventory management.
In essence, the MRP process allows organizations to navigate the often turbulent waters of production scheduling. The challenge lies in coordinating various inputs to ensure materials are available for production, thus preventing delays and excessive costs. The stakes are high; a misstep here can lead to bottlenecks or overstock, affecting the bottom line. Hence, grasping how this process operates not only helps in avoiding pitfalls but also focuses on leveraging MRP to its fullest potential.
Data Collection and Input Preparation
The initial phase of the MRP process hinges on accurate data collection and meticulous input preparation. The foundation of effective MRP relies on detailed and precise data regarding the inventory, lead times, and production schedules. Without a robust understanding of these elements, the system may produce results that might be more misleading than informative.
- Bill of Materials (BOM): Understanding each component necessary for a product's manufacturing is crucial. The BOM outlines all materials needed, including subassemblies and components.
- Inventory Records: Having updated inventory records ensures the MRP can assess the availability of materials. If records aren’t current, decisions made can be based on incorrect information.
- Master Production Schedule (MPS): This schedule details what needs to be produced and when. Without it, the MRP system will lack the directions necessary for planning production.
The preparation of these inputs often involves collaboration across different departments. For instance, the production team must communicate with purchasing and inventory management to ensure the data is consistent. As it goes, the clearer the picture painted by this data, the smoother the subsequent steps in the MRP process.
MRP Calculations
Once data has been collected and inputs are prepared, the next phase is the MRP calculations. This juncture incorporates mathematical formulas to determine how much material is needed, when it’s needed, and whether any adjustments are necessary. It's like having a finely tuned machine; each cog must fit perfectly to ensure functionality.
The main outputs of these calculations include:
- Net Requirements: Calculating the difference between what is needed and what is available.
- Lead Times: Understanding how long it takes for each material to be available after an order is placed ensures that production is not left hanging.
MRP calculations employ algorithms that assess various scenarios based on the collected data. This component of the process emphasizes the need for accuracy. Flawed data inputs can lead to cascaded errors, translating to improper material orders, which can significantly affect the overall production schedule.
Generating Production Recommendations
The final stride in the MRP process is generating actionable production recommendations. This step is tantamount to a well-orchestrated concert, where the calculations play the notes, and the recommendations harmonize to create a cohesive production strategy. Here, the MRP system pulls together all the input data and calculations to present recommendations about how to proceed.
The output typically consists of:
- Planned Orders & Releases: These dictate the amount and timing of materials needed for production.
- Exception Reports: Highlight discrepancies between needed and available materials, allowing managers to make informed decisions quickly.
By transforming calculated data into clear production recommendations, organizations can effectively align their manufacturing processes with market demands. This synchronization helps in maintaining a balance between meeting customer expectations and managing inventory levels.
In today's competitive landscape, effectively executing the MRP process offers a compelling advantage, enabling companies to respond swiftly to changing demands while keeping operational costs in check.
Outputs of MRP
In the world of manufacturing and inventory management, the outputs of MRP systems serve as the lifeblood of effective production planning. These outputs directly influence an organization's operational efficiency and help in aligning production schedules with market demands. The importance of these outputs cannot be overstated—ensuring that manufacturing processes are as smooth as a well-oiled machine is essential for staying competitive.
Planned Orders
Planned orders represent the blueprint for production. These are forecasts created from the data collected in the MRP cycle and play a critical role in ensuring that production aligns with demand. By outlining what needs to be manufactured, when, and in what quantities, planned orders provide clear guidance to production managers.
Understanding how to read and interpret these orders is crucial. These orders not only contain the specifics of what to produce but also the timing and resource planning needed. For instance, if a business knows that a specific product needs more time to manufacture due to longer lead times, it can adjust its planned orders accordingly.
Though planned orders offer a guide, they require continuous monitoring and adjustments based on real-time data because the market can shift like quicksand. A solid grasp of these orders can help prevent bottlenecks before they occur, keeping the production floor humming.
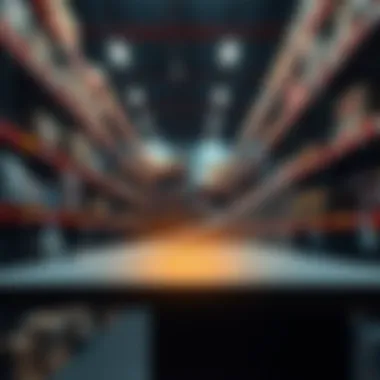
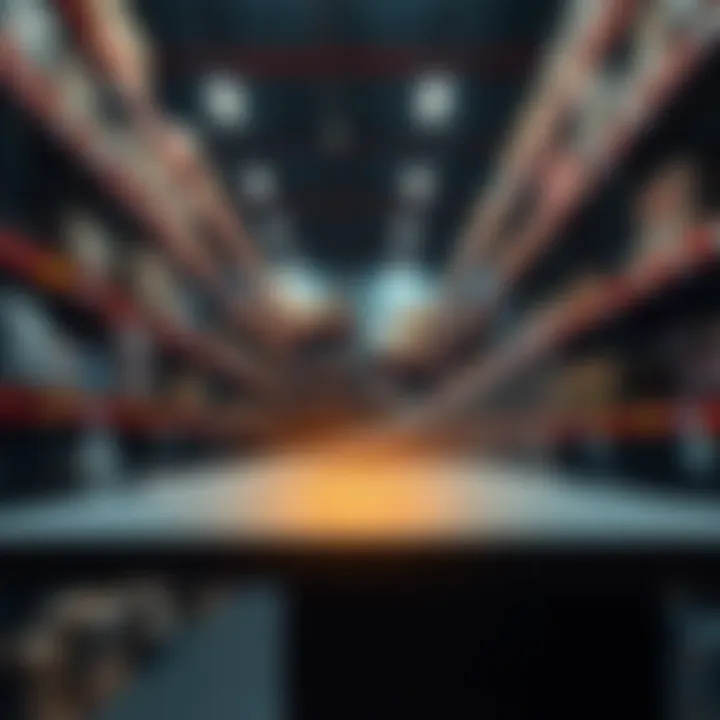
Order Releases
Following the planned orders, order releases are the actionable steps taken to initiate production. This is where the rubber meets the road. Order releases set production wheels in motion, officially communicating to the production team that it's time to start working on specific items.
These releases must be timely and precise to effectively sync with the scheduled planned orders. Poorly timed releases can create unnecessary idle time or worse, lead to missed deadlines. Therefore, understanding the cadence of order releases is fundamental. Effective coordination between purchasing and production teams ensures that materials are on hand when needed, preventing gaps in the production line.
A well-timed order release can mean the difference between meeting market demand and falling short in a competitive landscape.
Inventory Status Reports
Inventory status reports are paramount for tracking the flow of materials and finished goods throughout the production process. These reports provide insights into what is in stock, what needs replenishing, and when products will be available to meet incoming orders. It is like having a compass in the often-chaotic sea of inventory management.
By analyzing these reports, managers can identify excess stock that could tie up capital unnecessarily or pinpoint stock shortages that could disrupt production schedules. Keeping an eagle eye on inventory status allows companies to remain lean and efficient, thereby improving response times to customer demands and minimizing waste.
Performance Evaluation Metrics
At the end of the day, measuring the efficacy of an MRP system hinges on performance evaluation metrics. These metrics are essential for tracking how well the system is functioning and the extent to which it meets production goals.
Key performance indicators such as production lead times, order fulfillment rates, and inventory turnover provide a snapshot of operational health. By utilizing these metrics, businesses can not only identify areas of strength but also spotlight facets requiring improvement.
Role of Technology in MRP
In the digital age, the role of technology in Material Requirements Planning (MRP) cannot be overstated. As businesses strive to become more efficient, technology—specifically software solutions, enterprise resource planning (ERP) systems, and data analytics—becomes central to optimizing MRP processes. Technology facilitates seamless integration, enhances accuracy, and enables real-time decision-making. The benefits of implementing technological solutions in MRP processes are numerous; they range from improving production schedules to enhancing overall inventory management.
MRP Software Solutions
MRP software solutions are essential tools for manufacturers looking to streamline their operations. These programs allow companies to automate and refine their planning processes. They handle vast amounts of data, creating a structured approach to managing resources and production schedules. Notable features of such software often include:
- Planning and Scheduling: MRP software helps in calculating material requirements, aligning them with production schedules to avoid delays.
- Real-time Inventory Tracking: This capability ensures that businesses always have an accurate view of their inventory, which helps prevent overstocking or stockouts.
- User-friendly Interfaces: Many modern MRP solutions provide intuitive interfaces that simplify the user experience, enabling even non-technical staff to navigate them easily.
With the adoption of tools like SAP, Oracle, and Microsoft Dynamics, businesses gain a competitive edge through improved efficiencies and reduced human error.
Integration with ERP Systems
Integrating MRP with ERP systems provides a holistic view of all business functions, from finance to supply chain, making it easier to manage interdependent processes. When MRP is part of an ERP system, it benefits from shared data and coordinated processes. Key advantages include:
- Enhanced Visibility: The real-time sharing of information across departments ensures everyone is on the same page, resulting in better communication.
- Optimized Resources: An ERP-MRP integration enables companies to optimize their resource allocation by aligning production with real-time demand data, ultimately reducing waste.
- Streamlined Processes: By consolidating various functionalities into one system, businesses can reduce the complexity of their operations, leading to faster decision-making and improved agility.
Incorporating systems such as NetSuite or Infor can drastically enhance operational coherence.
Data Analytics in MRP
Data analytics plays an increasingly crucial role in refining MRP systems. With data becoming more abundant, leveraging analytics empowers companies to make informed decisions based on trends, forecasts, and actual performance. The strategic use of data analytics comes with notable benefits, including:
- Demand Forecasting: By analyzing historical data, businesses can predict future demand more accurately, improving their ability to plan and allocate resources accordingly.
- Performance Measurement: Analytics enables companies to assess their MRP performance metrics, adjusting strategies and processes based on data-driven insights.
- Risk Management: Understanding potential risks through data analytics allows organizations to prepare for fluctuations in demand or supply, enhancing resilience in challenging times.
"The future of manufacturing lies not just in having data, but in knowing how to use it effectively for smart, strategic decisions."
Challenges in MRP
Material Requirements Planning (MRP) systems provide a roadmap for efficient manufacturing and inventory management, but the landscape is not devoid of hurdles. Identifying and tackling these challenges is crucial for ensuring that MRP functions optimally. Understanding these difficulties can incite improvements, foster adaptability, and enhance the overall effectiveness of the MRP framework.
Accuracy of Data Inputs
One of the key challenges faced in MRP systems revolves around the accuracy of data inputs. These systems rely heavily on precise and timely information to generate effective material planning and scheduling. If the data is flawed—be it in inventory records, lead times, or demand forecasts—the consequences can spiral out of control.
For instance, if a company inaccurately records that it has more raw materials on hand than it does, it may inadvertently halt production or fail to meet customer orders. Inaccuracies can stem from varied sources:
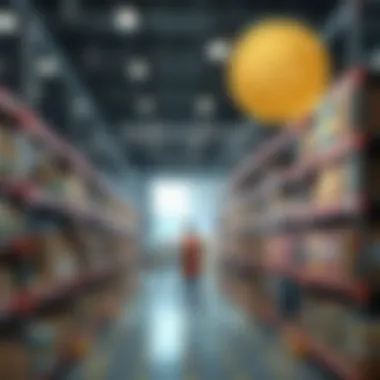
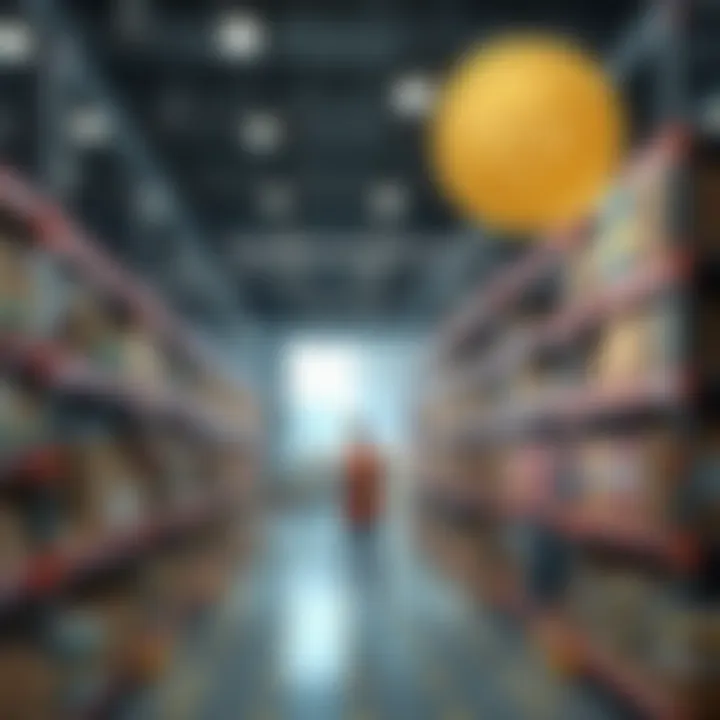
- Human errors during manual data entry
- Outdated inventory records that haven’t been synchronized with actual stock levels
- Miscommunication among various departments, leading to conflicting information
To combat inaccuracies, companies can implement rigorous data validation practices and regular audits of their inventory systems. Training staff to appreciate the critical nature of data integrity is also vital. In this data-driven age, accurate inputs are not just beneficial; they are fundamental.
Dynamic Market Conditions
The manufacturing landscape is as volatile as a ship in choppy waters, influenced by fluctuating customer demands and evolving market trends. This dynamism poses significant challenges to MRP systems, which often rely on historical data for projections and planning. When unforeseen changes occur, like sudden spikes or drops in demand, the MRP must be agile enough to adapt.
A notable example could be seen in the tech industry, where demand for certain electronic components may skyrocket due to a new product launch. If an MRP system relies solely on past sales data, it may underestimate the need for those components, leading to production delays. Conversely, if a recession hits, and consumer spending drops, the same system might overproduce, resulting in excess inventory that just sits there collecting dust.
To enhance responsiveness, organizations can integrate real-time analytics into their MRP to assess demand trends continuously. This way, companies can pivot quickly, adjusting production plans and stock levels in response to market cues.
Change Management in Implementation
Implementing MRP systems is not merely a plug-and-play scenario; it requires a thoughtful approach to change management. As new processes and systems are integrated, resistance from staff can develop, leading to gaps in execution and potential failures of the MRP.
It's essential to recognize that compatibility with existing workflows is crucial. A less-than-savvy implementation results in frustration and confusion among employees, which could turn a well-designed MRP setup into a sinking ship. To mitigate such fallout, companies should focus on:
- Developing a clear communication strategy that outlines the benefits and changes associated with the new system.
- Providing comprehensive training for employees, allowing them to grasp the ins and outs of the new MRP.
- Involving staff in the decision-making process to ensure their concerns are heard and addressed.
Implementing MRP is a journey, not a destination. By managing the change sensitively and strategically, businesses will be well-prepared to optimize their production planning and inventory control, leading to improved efficiency across the board.
In the world of MRP, overcoming challenges is part of the process, acting as stepping stones toward operational excellence.
Future Trends in MRP
Understanding future trends in Material Requirements Planning (MRP) is pivotal for any business looking to stay ahead in today's fast-paced market. As manufacturing environments become increasingly complex, recognizing how MRP will evolve helps in making informed investment and operational decisions. Companies are not just relying on traditional methods anymore; they are innovating and adapting to technological advancements that could drastically change the way they plan and manage resources.
Artificial Intelligence and Machine Learning
One of the most significant shifts in MRP is the integration of Artificial Intelligence (AI) and Machine Learning (ML). These technologies offer a tremendous advantage in data analysis, allowing for more accurate forecasts and enhanced decision-making capabilities.
- Predictive Analytics: Using historical data, algorithms learn patterns to predict future demands more accurately. This shifts the focus from reactive to proactive planning, reducing waste and optimizing inventory levels.
- Automation of Routine Tasks: AI can take over repetitive tasks, freeing up personnel to focus on strategic initiatives rather than day-to-day operations. This capability allows for significant labor cost savings.
The implications of this are enormous. Businesses can expect reduced lead times and improved customer satisfaction as they can respond more agilely to fluctuations in demand. Furthermore, the capacity to adapt quickly can be the difference between thriving and merely surviving in a competitive marketplace.
Real-time Decision Making
Another key trend is real-time decision-making capability, driven by cloud computing and continuous data feeds. In the past, MRP systems relied heavily on static data inputs, which could lead to aging information and delayed responses. However, with ongoing access to live data, businesses can make immediate adjustments to their production schedules and inventory levels.
- Enhanced Visibility: The transparency afforded by real-time data allows for a holistic view of operations. Decision-makers can analyze the status of inventory and production simultaneously, leading to faster and better-informed decisions.
- Collaboration Across the Board: Teams no longer work in silos. Real-time data encourages collaboration among suppliers, manufacturers, and distributors, facilitating a cohesive approach.
"The ability to pivot quickly in response to market changes is no longer a luxury; it’s a necessity. Companies integrating real-time decision-making into their MRP processes will undoubtedly have an edge."
With these insights in mind, investors, financial advisors, analysts, accountants, and entrepreneurs should remain vigilant to the developments in MRP, ensuring they leverage these innovations effectively.
Epilogue
In summary, the conclusion serves as the bedrock of the entire discussion on Material Requirements Planning (MRP). It encapsulates the pivotal points raised throughout the article, highlighting both the direct and indirect benefits that can be accrued from a thorough comprehension of MRP systems. Notably, this section emphasizes the interrelation between key inputs and outputs, which fundamentally shape production strategies and inventory management.
Understanding MRP not only aids in predicting material needs efficiently but also ensures that businesses remain agile in an unpredictable market. The clarity of this process can dramatically influence decision-making practices, optimizing operational workflows, and enhancing financial forecasts. Therefore, every investor, accountant, and entrepreneur should recognize the critical nature of MRP in maintaining a competitive edge in their industries.
Summary of Key Takeaways
- MRP Principles: At its core, MRP is about ensuring the right materials are in the right quantities at the right time. The necessity of precise inputs, such as Bill of Materials (BOM) and Master Production Schedule (MPS), cannot be stressed enough.
- Efficiency and Cost Reduction: Effective use of MRP can significantly reduce wasted materials and inventory costs, leading to better financial performance.
- Technological Integration: Modern MRP systems rely heavily on advanced software and integration with ERP systems, boosting accuracy and real-time decision-making capabilities.
- Market Responsiveness: Organizations employing MRP can adapt more swiftly to changes in demand or supply chain disruptions, a critical advantage in today’s fast-paced market.
- Data Quality: Accurate input data directly impacts the output of the MRP process, making data integrity crucial for operational success.
Implications for Investors and Businesses
For investors, the implications of understanding and implementing MRP systems within an organization are profound. Companies that effectively harness MRP practices can exhibit improved operational efficiency, which traditionally translates into better margins and return on investment. Thus, potential investors should keenly evaluate a company's MRP capabilities when considering investment opportunities.
For businesses, the knowledge gleaned from this understanding allows leaders to enact strategic initiatives aimed at cost reduction and operational optimization. The implications extend beyond basic inventory management; they spur innovation in production processes and encourage proactive approaches to demand forecasting. In navigating complexities like fluctuating market conditions, businesses that prioritize MRP practices are positioned advantageously, fostering resilience and sustainability.
"Investing in robust MRP systems is akin to laying a foundation for long-term success in manufacturing and supply chain management."